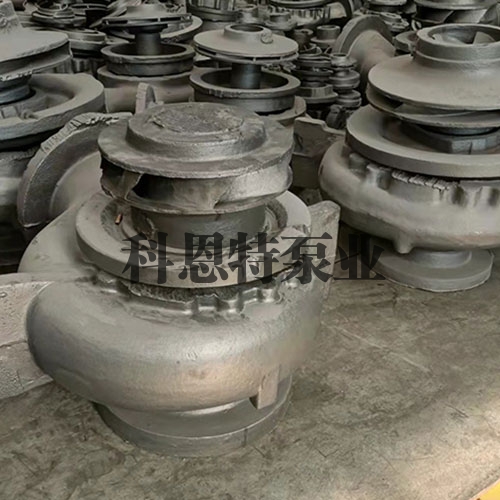
Investment casting, also known as "wax loss casting", usually refers to the casting process where a mold is made from a fusible material, and several layers of refractory material are coated on the surface of the mold to form a shell. The mold is then melted and discharged from the shell to obtain a mold without a parting surface. After high-temperature roasting, it can be filled with sand for casting. Due to the widespread use of wax materials in the production of patterns, investment casting is often referred to as "wax loss casting".
The types of alloys that can be produced by investment casting include carbon steel, alloy steel, heat-resistant alloy, stainless steel, precision alloy, permanent magnet alloy, bearing alloy, copper alloy, aluminum alloy, bowl alloy, and ductile iron. The shape of investment castings is generally quite complex, with the minimum diameter of holes that can be cast on the casting reaching 0.5mm and the minimum thickness of the casting being 0.3mm. In production, some components that were originally composed of several parts can be designed as a whole with zero polarity by changing the structure of the parts, and directly cast by smoke buried casting to save processing time and metal material consumption, making the structure of the parts more reasonable.