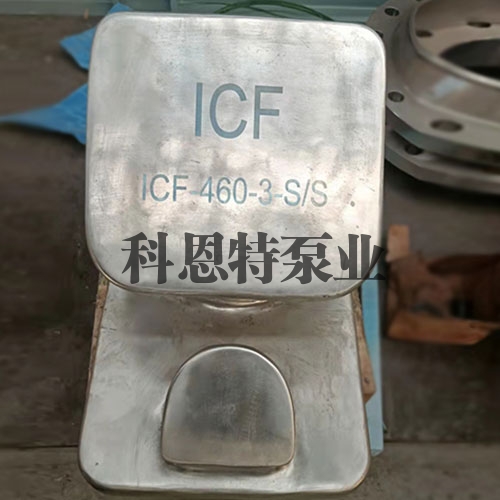
Metal mold casting, also known as hard mold casting, is a casting method that pours liquid metal into the metal mold to obtain castings. Molds are made of metal and can be reused multiple times (hundreds to thousands of times). The castings that can be produced by metal mold casting have certain limitations in terms of weight and shape, such as only simple shaped castings for black metal; The weight of the casting should not be too large; There are also limitations on wall thickness, and smaller castings cannot be produced.
There are significant differences in performance between metal molds and sand molds. For example, sand molds have breathability, while metal molds do not. Sand molds have poor thermal conductivity, while metal molds have good thermal conductivity. Sand molds have yielding properties, while metal molds do not. These characteristics of metal molds determine that they have their own patterns in the formation process of castings.
The impact of gas state changes in the mold cavity on casting forming: When metal is filled, the gas in the mold cavity must be quickly discharged, but the metal has no permeability. Any slight negligence in the process can have a negative impact on the quality of the casting.
The characteristics of heat exchange during the solidification process of castings: Once the molten metal enters the mold cavity, it transfers heat to the metal mold wall. Liquid metal loses heat through the mold wall, undergoes condensation and contraction, while the mold obtains heat and increases temperature while expanding, resulting in the formation of a "courtyard" between the casting and the mold wall. Before the "casting room metal mold" system reaches the same temperature, the casting can be regarded as cooling in the "gap", and the metal mold wall is heated through the "gap". The impact of metal mold shrinkage on the casting: the metal mold or core, without yielding during the solidification process of the casting, hinders casting shrinkage, which is another characteristic of it.